|
|
|
Newby Foundries - Legacy, Total Quality & Investment in Shell Foundry |
|
|
Established over a century ago Newby Foundries Ltd. is a market leader in the supply Ductile Iron castings. Our Total Quality culture, is supported by our accreditation to ISO/TS 16949:2002.
In recent years, the company has undertaken a significant investment in totally modernising our shell foundry. Our strengths are our flexibility and product diversity, enabling us to satisfy our customers’ wide ranging needs.
We place considerable importance on the quality and development of our workforce and, to this end, we hold the ‘Investors In People’ standard to ensure that we have sufficient competent staff, adequately trained for both existing and long term needs.
Visit the Newby Foundries website - follow the link below. Newby Foundries - for Shell Moulded Castings, Grey Iron Castings etc. |
Range of Products inc. Shell Castings |
|
|
Examples of cast components. Newby Foundries produce castings to a range of industries; in particular to pump, valve, hydraulic and turbocharger manufacturers. Castings are produced in the full range of Grey, Ductile, Austenitic and Alloyed Irons to internationally recognised standards. We can also supply to customers own requirements. Visit the Newby Foundries website - follow the link below. Newby Foundries - for Shell Moulded Castings, Gray Iron Castings etc.
|
Design of Castings and Simulation of the Metal Flow & Solidification |
|
|
Design & Simulation
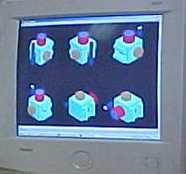 |
|
The use of state of the art high-speed computers, along with the most advanced software enables our methods engineer to accurately simulate both the flow of molten metal within the mould cavity, and the subsequent solidification characteristics. This is an invaluable tool in minimising pattern development time and ensuring a “Right first time” methoding solution. Potential problems such as, shrinkage porosity, cold laps, and misrun can be identified and resolved without the need for costly and time consuming pattern, mould and casting production. Our in house casting design team provides informed advice on casting design, materials and process selection, to identify at the onset of a project the optimum casting solution, and minimise the lead time to market.
Visit the Newby Foundries website - follow the link below. Newby Foundries for hydraulic valve castings, pump body castings etc. | |
Rapid Prototyping in Resin |
|
|
Rapid Prototyping
The foundry production development department also uses rapid prototyping facilities to help assess casting shape for manufacturing. RP models can also be used to create low budget tooling producing prototype castings for testing and appraisal.
Visit the Newby Foundries website - follow the link below. Newby Foundries for shell moulded castings, nodular/ sg iron castings etc. |
Global Sourcing from Local Experts |
|
|
‘Newby Foundries can globally source, and supply fully finished castings to your requirements .’
To complement this service we can also procure your tooling requirements and liase with your design engineers at the concept stage to make sure that, together, we can successfully supply you with castings in any grade and material to whatever finish you require. This would be offered with the full backing of the Newby quality standards of inspection and delivered to whatever destination you require. The advantages of sourcing through Newby Foundry are: • We assess and vet sub-contractor/supplier. • We inspect and guarantee the quality and delivery of castings to, you, the customer. • Any initial sampling, tooling verification, PPAP or any other issues become our responsibility. • All components quoted can be either raw castings, semi-finished or fully painted and machined ready for assembly. • We can provide all testing and certification. • Stocking and KanBan agreements can be negotiated.
Visit the Newby Foundries website - follow the link below. Newby Foundries - Vacuum backed shell moulded casting foundry. |
Finishing - Robotic Fettling |
|
|
Robotic fettling at Newby Foundries
 |
|
Finishing Facilities - Robotic Fettling
Newby Foundry has commissioned the installation of two automated robotic
fettling stations. Advantages
- Consistent grinding profile
- Constant and reliable output
- Does not require skilled operators
- Higher output
- Can grind accurate reference locations for
other operations
- Improved workshop environment
|
|
Quality Department
Through carefully developed operating procedures our quality standards are continuously being raised. The Mark-Out department is equipped with a computer assisted 3 axis co-ordinate measuring machine (C.M.M.) This set-up allows us to dimensionally assess tooling and sample castings to PPAP requirements quickly and accurately. Printed results of findings can be generated for customer approvals. Our Quality Department is supported by well equipped laboratory facilities, enabling us to carry out spectrographic analysis, mechanical and non-destructive testing including dye-penetrant, ultrasonics, magnetic particle and endoscopy.
Visit the Newby Foundries website - follow the link below. Newby Foundries for shell moulded castings, nodular / sg iron castings etc.
|
Shell Mould & Vacuum-backed Shell Foundry |
|
|
NEWBY FOUNDRIES - Vacuum Backed & Conventional Shell Moulding Smith Road, Wednesbury, West Midlands. WS10 0PB.
Commissioned in 1992, this purpose built Shell Foundry provides Newby Foundries with a modern facility that is accredited to ISO/TS 16949:2002, and underpins our position as a leader in this method of manufacture. Shell Moulding produces castings with close dimensional tolerances, good surface finish and excellent reproduction of detail. The process often reduces the amount of subsequent machining, assembly and finishing when compared to conventional moulding. Our design team can help you explore and maximise these opportunities. Vacuum Backed Shell Moulded castings offer all the benefits of the standard Shell Process with the ability to cast larger more complex castings up to 90Kg. This process is based on the support of the shell moulds using the latest Vacuum Technology. Increased Rates of gas removal and very low fume emissions are also benefits of this Unique Process.
Weight Range: |
0.25kg - 25kg (Standard Shell Process) & 20kg - 90kg (Vacuum Backed Shells) |
Melting Facilities: |
4 - 1/2 Tonne Induction Furnaces |
Heat Treatment: |
Own Heat Treatment Facility. |
Certification: |
Provision of non-destructive test certificates as required. |
Vacuum Backing Plant
Visit the Newby Foundries website - follow the link below. Newby Foundries - Vacuum backed shell moulded casting foundry. |
Phoenix House, Smith Road, Wednesbury, West Midlands. WS10 0PB.
Tel : +44 (0)121 556 4451 Fax : +44 (0)121 505 3626
|
|
|